设备润滑管理十大误区
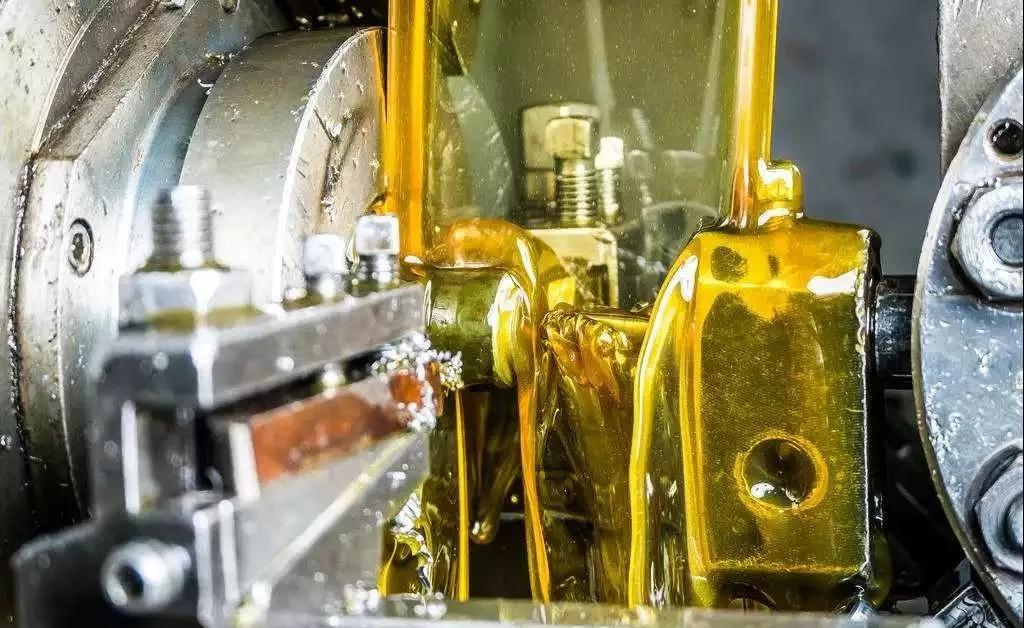
误区一
设备润滑管理组织机构不健全,润滑管理人员换人频繁
润滑管理带来的效益是滞后的、长期的,企业缺乏润滑管理长期计划,组织机构松散;设备管理部门只管设备的现场用油,对设备的用什么油说了不算,对进厂新油及在线设备用油的检验没有统一管理;润滑管理员(润滑工程师)不稳定,换人频繁。这是企业在润滑管理上的一大失误。
误区二
现场油品污染,加速设备失效
此问题比较突出,缺乏润滑知识,大型设备检修时间紧,没有清理换油时间,不能够系统清洗换油,长时间只补油不换油,油品污染严重,既有水又有粉尘及磨损颗粒,加速了设备磨损;现场设备润滑卡片长期不换,加油工具无标识,油桶混用。
误区三
设备的选油不规范,加速设备失效
此问题主要表现在进口设备及蜗轮蜗杆齿箱的润滑用油,选油上只从价格上考虑,没有考虑进口精密设备体积小传动力矩大,一般矿物油承受不了大的负荷造成备件磨损;再就是蜗轮蜗杆齿箱的用油,蜗轮蜗杆齿箱主要是滑动摩擦,还有滚动摩擦,蜗轮为铜质,选用一般矿物极压齿轮油。一般矿物油极压添加剂中主要成分是硫、磷离子,硫、磷与蜗轮蜗杆齿箱中的铜蜗轮有很强的腐蚀性和攻击性。工作在高滑动摩擦,极压添加剂的腐蚀破坏了齿轮表面的完整性,极大地增加了蜗轮表面摩擦系数,随后的金属表面间的接触和滑动造成了灾难性的磨损。
误区四
没有开展设备润滑油品检测,没有监测就没有控制
开展油品理化指标检测的企业为数不多,国内有大小润滑油企业4000多家,良锈不齐、鱼目混珠,企业缺乏润滑油品监测中心或者监测站。对进厂的新油没有进行理化指标检测,就无法说明此油是否合格,进厂新油控制不住,在线设备用油不检测,就无从谈起设备润滑管理。这就是长期以来养成的换油不清洗油箱油路的主要原因,没有监测就不能说明油品污染变质。
误区五
大型设备缺乏油品在线过滤系统
设备的管理者认为稀油站回油管路中的过滤器就是过滤油中污染颗粒的,其实不然,此过滤器只能过滤粒度在100μm以上的大颗粒。有的设备新安装时有过滤系统,但存在着长期不换滤芯现象,正常使用中存在,一、不知何时换滤芯,二、换滤芯时不按要求的滤芯精度换。
误区六
现场没有专职的润滑工,加油工作由操作工负责
通过油液分析发现设备用油中出现混油现象,出现这种现象查原因和责任人都没有办法,因为一台设备需要一个岗位的最少四名操作工来负责加油,到底哪个班加错油了?不好查,查不出原因就不好整改,还有加油工具混用不规范。
误区七
新建项目设备用油由施工单位自行采购,缺乏有效的监督
企业新扩建项目中设备用油,是由施工单位自行购买润滑油品,不同生产厂家的润滑油品的价格相差很大,而负责施工管理的人员又不了解润滑知识,施工单位会以次代好、以低代高,造成设备因用油不当造成前期磨损,甚至发生重大设备事故。
误区八
没有开展设备润滑磨损状态监测
部分大型企业虽然开展了油品检测,只是对进厂新油和在线油品的理化指标的检测,只能对油中水分、机杂、粘度、酸值的变化进行检测。而国外已普遍采用ISO 4406-99污染度标准检测油中污染颗粒,通过自动颗粒计数器计数油中颗粒的大小和多少,控制油中污染,减少零件磨损。目前,国外已把污染监测看作是最重要的润滑油的监测项目,而我国还在使用“机杂”检验油中颗粒的百分比。开展磨损状态监测的单位就微乎其微,所谓油液状态监测就是通过监测仪器监测油中摩擦副的磨损情况,通过光谱分析了解磨损的成分和颗粒的大小及含量。做定期跟踪分析,做到预知设备检修、做到视情检修。比如:铁铺分析、光谱分析。
误区九
新材料的推广难度大,设备选油谁来定
设备选油是最大的难题,国有企业都存在同一个问题,这也是国有企业在润滑管理上存在的共同弊端。设备该用什么油由谁说了算呢?国外的润滑工程师理所当然地对设备用油说了算,但国内企业设备用油由供应部门说了算。
误区十
设备润滑管理无培训计划
最近几年润滑技术在飞速发展,企业安排润滑工程师和部分设备管理人员外出参加设备润滑交流会议,虽然得到部分知识,但大部分的设备管理人员没有参加培训。缺乏内部培训计划,设备管理人员对固体颗粒、水分在油中存在对设备有多大危害不知,甚至,油粘度如何选用不了了之,造成设备混油。不了解润滑知识,设备润滑选油、何时换油就无从谈起,只有对设备频繁抢修和检修。
来源:网络
(本文来源为外部转载,本网对文章内容不承担任何责任)
下一篇:变速箱漏油怎么办?
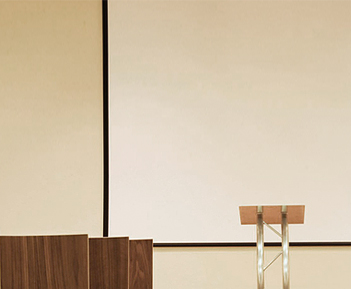
业务咨询
维鼎化工业务部
- 邮件:xushusheng@windin.net
- 销售:许先生 0755-2698 5826 、